1. Meaning of the first parameter in SECTION 9 DESCRIPTION OF LINES
As
explained in the manual
the first parameter in SECTION 9: DESCRIPTION OF LINES in an integer
which can have the values 0, 1, or 2. But it was only stated that
options 1 and 2 are not fully implemented. That is why it is advisable
to always use option 0 for all models, as we have done so far.
The reality is that now
there are
four usable options for the initial parameter: 0,1,2,3... This has been the case since many versions back
(!). The meaning of this "mysterious" initial parameter of SECTION 9 is
as follows:
0 = calculate the lines and their branches considering that the virtual
extension of each line, intersects the midpoint of the N attachment
points with which connects.
1 = calculate the lines and their branches considering that the virtual
extension of each line, intersects the midpoint of the N attachment
points with which connects, pondered by each chord length
2 = calculate the lines and their branches considering that the virtual
extension of each line, intersects the midpoint of the N attachment
points with which connects, pondered by each chord length and relative
rib weight parameter set in column 7 of SECTION 2.
3 = calculate the lines and their branches considering that the virtual
extension of each line, intersects the midpoint of the N attachement
points with which connects, pondered by each chord length, the relative
rib weight parameter set in column 7 of SECTION 2, and the distribution
of loads in the attachement points of a rib according to the
distribution selected in
SECTION 18.
Option 0, is what we have used so far. It is the easiest to understand
(simply each line naturally looks for the direction of the geometric
center of the fixing points located on the sail). For example riser A
is aligned with the geometric center of all attachments that connect to
A. This is simply a conjecture, but it works, as shown in the real
world.
Option 1, make a weighted average, considering only the chords lengths.
That is, considering that the lift of each profile is proportional to
the length of its chord. Of course, the central profiles support more
load than those located towards the wing tips. Optimization spanwise.
Option 2, make a weighted average, considering the lengths of the
chords and their relative weights, defined in column 7 of SECTION 2.
Normally, the defined values are 1.0 (and can be defined as such, for
all models). But, in some cases would be interesting to indicate
relative weights of 2.0 or 3.0, when we use diagonals that allow to
jump two or three cells and logically the load increases proportionally
with respect to other zones with attachments in each profile (relative
weight 1.0). Improved spanwise optimization.
Option 3, It is the most complete and recommended. Makes a weighted
average using options 1 and 2, and also the percentage
distribution of the loads in each profile, according to its number of
attachments, according to SECTION 18. Thus, section 18 is not only used for
elastic corrections and for informative calculation of loads at each
attachment, but also for the perfect orientation of branches in space.
In practice, using option 3 is very easy!
Just type a "3" (instead of "0") in the first line of SECTION 9.
The values given in section 18 can be considered invariant (approximate
enough for all wings), although you can change to adjust to your
preferences or profile types. The relative weights in column 7 of
section 2 can be defined as "1.0" or slightly modified if you use mixed
cell jumps. Optimization spanwise and chordwise.
If you use option 3, it is also recommended to run the program once
with option 0 to verify the differences. You can overlay 3D line models
with different colors in the DXF 3D model or compare line listings. For
example, in the case of the BHL5-16 model I checked for differences of
up to 2.3 cm. It is expected that the calculation made with a weighted
distribution type 3 will provide more solidity to the wing (without
being able to quantify at this time the improvement obtained). In model gnuA6-32 the differences are up to 4 cm.
The ramifications of the brakes are always calculated by default
according to model 0 (geometric), since the forces are applied directly
by the pilot.
2. Minimal test example
We have created a minimal "paraglider" of only 3 cells and 4 ribs, to verify the effect of the parameters.
Input files:
***************************************************
* 9. SUSPENSION LINES DESCRIPTION
***************************************************
3
<<< Parameter "3"
3
2
3 1 1 2 1 3 1 0 0 1 1
3 1 1 2 1 3 2 0 0 1 2
2
3 1 1 2 1 3 1 0 0 2 1
3 1 1 2 1 3 2 0 0 2 2
4
3 1 1 2 1 3 1 0 0 3 1
3 1 1 2 1 3 2 0 0 3 2
3 1 1 2 1 3 3 0 0 4 1
3 1 1 2 1 3 4 0 0 4 2
Forced sections:
**************************************************************
*
2. AIRFOILS
*
**************************************************************
* Airfoil name, intake in, intake out, open , disp. rrw
1 gnua.txt 1.6
6.3 1 0
30 15
<<< relative rib weight 30 (!) in column 7. Normal vaule = 1.0
2 gnua.txt 1.6
6.3 0 0
1 1
Load distribution in % SECTION 18:
*****************************************************
* 18. Elastic lines corrections
*****************************************************
100
75
25
<<< A=75% B=25% (2-liner)
40
40
20
<<< A=40% B=40% C=20% (3-liner)
40
40 20
0
<<< A=40% B=40% C=20% D=0% (4-liner, forced; normal 35 35 20 10)
35 35 15 10 5 <<< A=35% B=35% C=15% D=10% E=5% (5-liner)
1 0.08 0.2 0.2
2 0.08 0.2 0.2
3 0.08 0.2 0.2
4 0.08 0.2 0.2
5 0.08 0.2 0.2
Results:

01 Model parameter "0". Line C (green) passes through the geometric center of the attachments C and D.
|

02 Model parameter "3" forced using
load distribution A=40% B=40% C=20% D=0%. Since it has been assumed
that attachment D does not support load, the green bifurcation
continues straight until C
|

03 Frontal Model 0.
|
04 Model type "3" forced using
relative weight in rib 1 30 times higher than the rib 2 (exaggerated in
order to verify the effect).
|
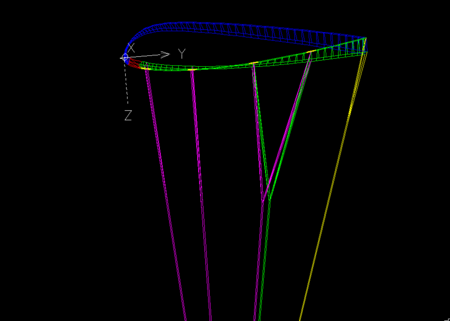
05 Comparative model "0" and model "3"
natural in magenta (not forced). It makes sense for line C to move
forward, since C attachment point supports less load than D.
|
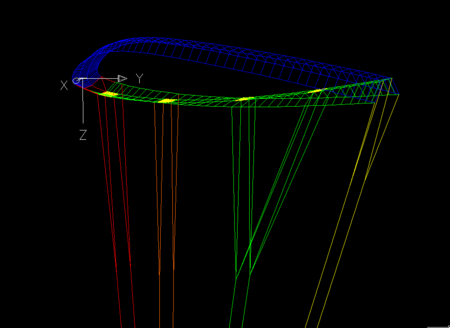
06 Test 3 natural 3D
|
Parameters 0,1,2,3 now can be used with lep-3.16 and several previous
versions. However it will be from lep-3.17 that it will be officially
incorporated. Some additional checks need to be made, on the operation
of the relative weights of column 7 of SECTION 2. Using values 1.0 in
column 7 the results will already be very accurate. As stated above, it
is recommended to compare with the simplified model 0 (figure 05).